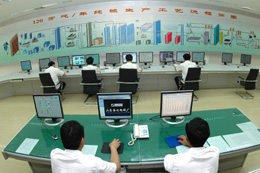 |
|
山东海化集团纯碱厂是亚洲同行业中首家采用国际领先的先进过程控制技术实现中央集中控制的企业。他们自主开发了具有国际领先水平的MES系统,该系统使生产的各种流程图、历史曲线、消耗、考核、故障诊断等情况在电脑上一目了然,能根据一项指标要求自动调节各相关指标,实现了远远胜过人工的智能模糊控制。张勤业
摄 |
| 走进山东海化集团生态工业园,登高远望,只见一处处企业、一座座厂房之间都有管道相连,绵延十多里,蔚为壮观。这些企业借助管道,形成了一个个能源、资源的综合利用循环圈。
“能”尽其力
“纯碱厂和热电分公司之间只通了一条管道,一年回收的余热就折合原煤3.3万吨。”在海化热电分公司,总工程师李金风介绍说,热电需用的清水经过预热达到一定温度时,才能进入化学水处理工序,但预热需要消耗大量的热能,而纯碱厂的碳化塔需用海水进行工艺冷却。经过科学论证,他们就架了一条管道,先将清水送纯碱厂,在给碳化塔冷却的同时吸收其反应热,加温预热后再送热电化学水处理,这样一年下来,不但回收余热折合原煤3万多吨,而且还为纯碱厂节约海水1000万立方米,节电350万千瓦时。 这是海化集团科学利用化工余热的一个缩影。他们对装机总容量21万KW的热电分公司产生的废热和化工装置产生的余热进行统筹规划,梯级开发,实现了余热和废热的循环综合利用。 以炭黑为主要产品的海化炭黑公司,排出的尾气中含有60%的一氧化碳和部分硫化氢等气体,每立方米尾气燃烧能产生600多大卡热值。如果将这些尾气排到天空中,既污染环境,又浪费热能。 经过科学论证,海化集团决定与韩国东洋制铁化学有限公司合作,由韩方投资850万元,在二电厂实施炭黑尾气掺烧工程,将炭黑尾气全部用管道送到二电厂锅炉炉膛,与煤掺烧充分燃烧,用于产汽、发电。据介绍,工程投用后每小时可利用炭黑尾气5.3万立方米,一年可节约燃煤5万吨,真正做到了节约资源、变废为宝。
“水”畅其流
海化集团地处北部沿海,淡水供需矛盾突出。化工生产是用水大户,生产过程中会产生大量的废水,海化集团通过一水多用、循序循环用水、技改节水等措施,对产生的废水进行综合利用,使“废水”变成了“肥水”。 在山东省节水型企业——海化热电分公司,生产技术部部长王宝田介绍说,他们投资500万元,修建了一个废水泵房和废水池,将纯碱厂和热电分公司产生的废水集中回收,经中和沉淀后再利用到热电厂冲渣、冲灰,目前,废水泵房全天候运行,每小时节约海水800多吨,年创效益700多万元。最近,这个污水综合利用工程被山东省建设厅评为山东省15个再生水利用示范项目之一。 目前,海化集团2006年度第一批15个节水技改项目即将全部结束,这些项目实施后,每年节约淡水288万立方米,年创效益1770万元。
“物”尽其用
在“循环经济”理念的催生下,一些看似“天方夜谭”的综合利用设想,在海化变成了生动的实践。 电石法PVC生产工艺中产生的电石泥废渣如何处理,一直是困扰行业发展的一个难题。电石泥的主要成分是氢氧化钙,而纯碱生产中恰好需用氢氧化钙作原料。海化集团把氯碱树脂公司产生的电石泥废渣送到与其毗邻的具有年200万吨生产能力的纯碱厂,全部用于纯碱生产,在国内率先实现了纯碱、氯碱在产业链上的“连理”,从根本上解决了聚氯乙烯树脂企业电石泥废渣环保利用的行业难题。 综合利用制碱废液,生产的产品销往国外,是许多纯碱企业一直追求的梦想。如今,海化把这一梦想变成了现实。海化经过科技攻关开发出综合利用制碱蒸氨废清液生产氯化钙工艺,将进入系统的废液全部利用,使制碱废液利用率达到100%,创造了世界制碱史上蒸氨废液不排海的先例。 在海化硫酸钾厂生产现场,面积达100多平方公里的盐场晒盐后的苦卤全部收集起来,通过地下管道汇集到硫酸钾厂,用来生产硫酸钾、氯化镁、氢氧化镁等产品,苦卤中的有用成分基本上就被“吃”尽了。2006年,海化集团从“三废”里“抠”出了2亿元综合效益,相当于全集团实现利润总额的25.6%。 据海化集团董事长肖庆周介绍,去年海化营业收入进入中国企业500强,位居第200位,名列中国化工企业第一位(不含石化、医药)。已有合成纯碱、硝盐、固体氯化钙三种产品产量居世界首位,原盐、三聚氰胺两种产品居亚洲首位,溴素、水玻璃等七种产品居全国首位,年进出口总额达三亿美元,成为全国最大的海洋化工产品生产和出口创汇基地。海化集团被国家发展改革委等六部委确定为全国首批循环经济试点单位之一,海化集团所在的滨海经济开发区被国家环保总局确定为国家生态工业示范园区。 |